The Importance of Specifying the Right Cable Cleat
7th Apr 2022
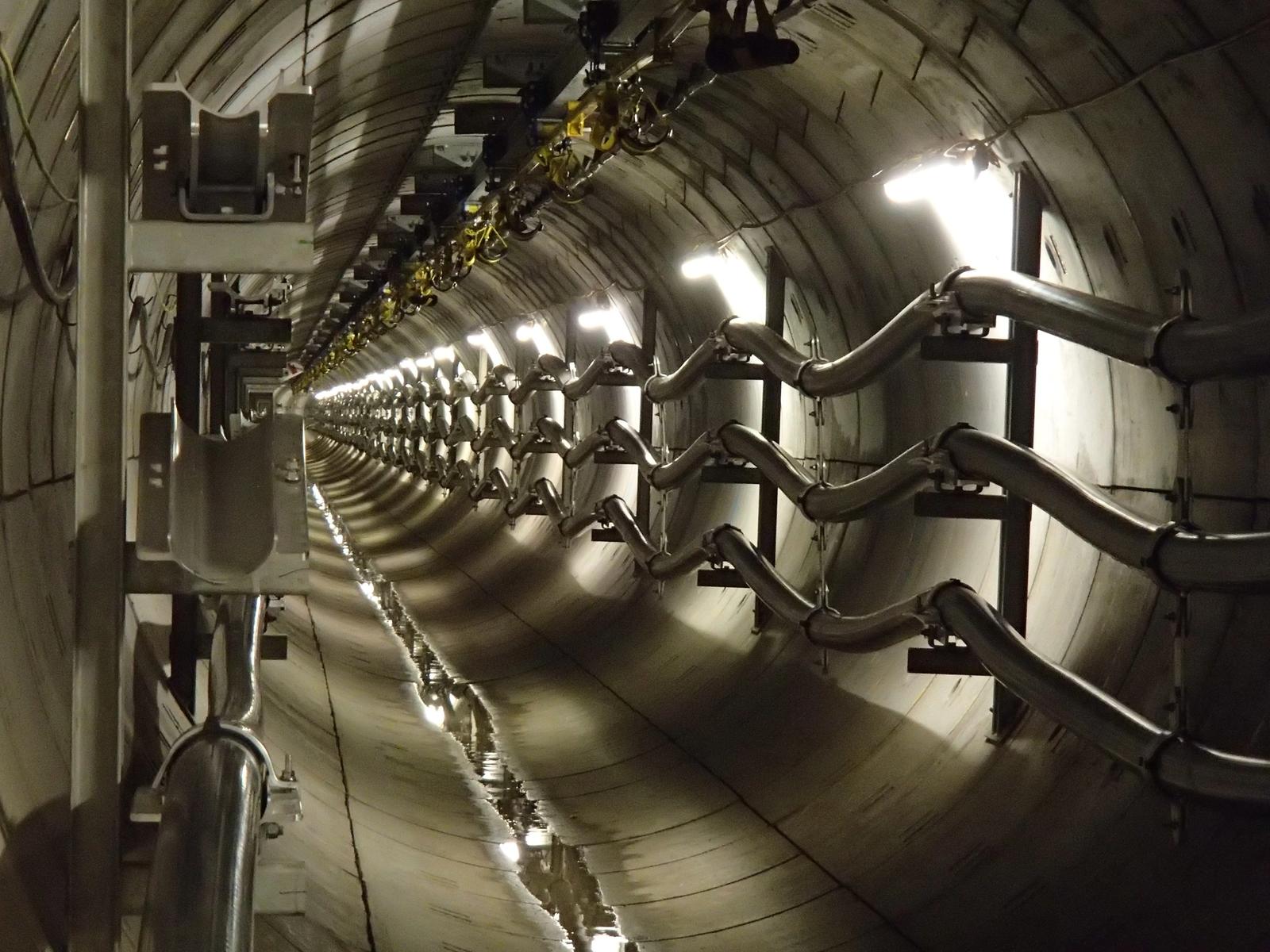
Pictured: ELLIS Patents Centaur Cable Saddle installed in National Grid's London Power Tunnels project.
ELLIS PATENTS Technical Article
First published April 6th, 2022
Cleat Class
The vital importance of cable cleats in electrical installations is now well known, but with this greater understanding has come a significant increase in the number of products on the market.
Kelly Brown, sales director of ELLIS Patents talks about the steps that need to be taken to ensure the right decision is made when specifying cable cleats.
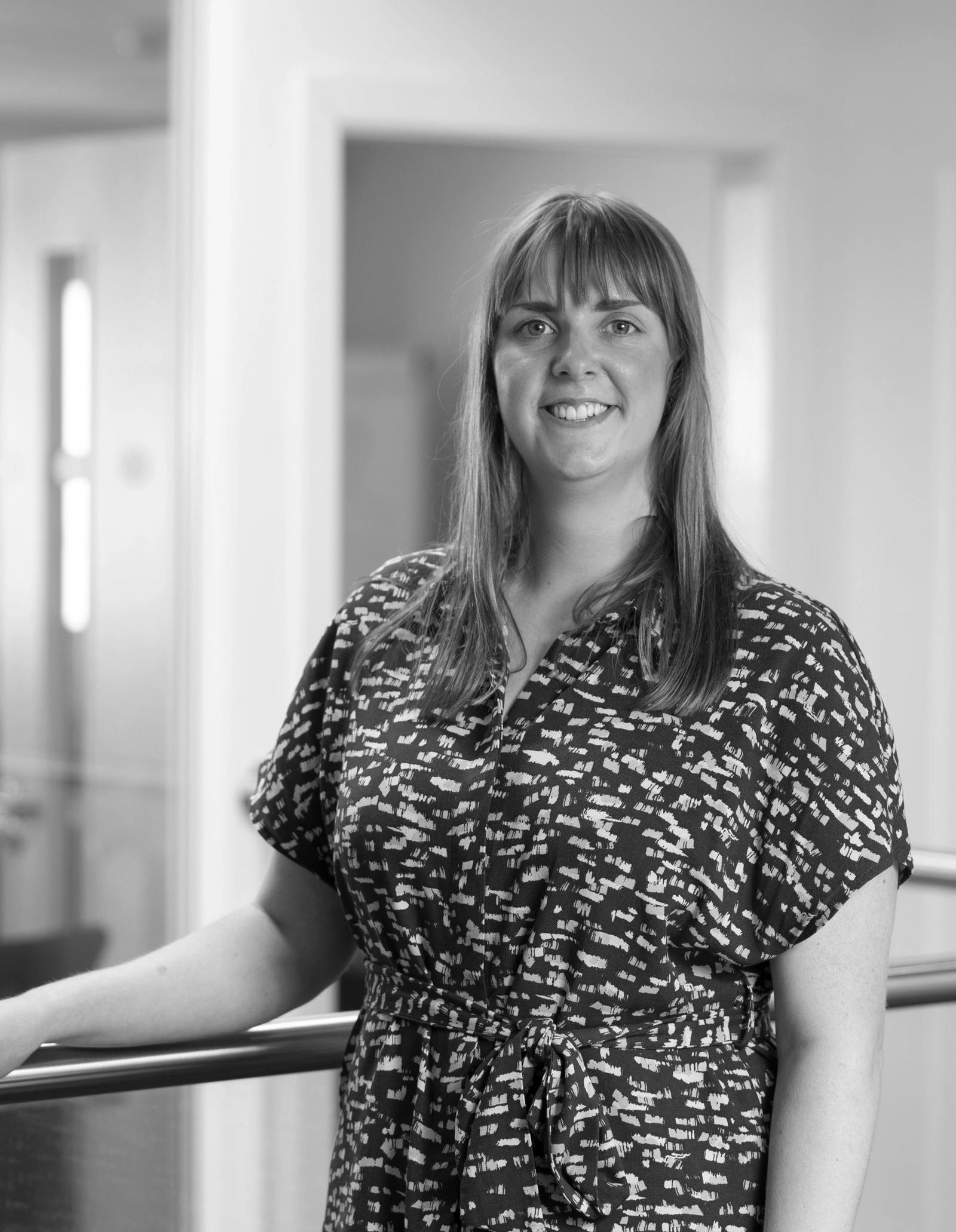
Pictured: Kelly Brown, Sales Director of ELLIS Patents.
For many years ELLIS Patents was the lone voice stressing the importance of correctly specified cable cleats, but today there are a growing number of manufacturers with the same message. Competition is, of course, good; not only does it give a customer choice, it also helps drive product development.
Unfortunately, in the cable cleat market this isn’t really the case. Instead, customers are now presented with numerous products of remarkably similar appearance, and in many cases products are being brought to market as computer renderings before they exist in reality. And while they say that imitation is the best form of flattery, it certainly makes a customer’s job harder when they have to sort fact from fiction in the specification process.
What all of this adds up to is that when specifying a safety critical product like a cable cleat, a buyer really should resort to confidence and trust when making their final decision.
So, what steps do you need to take when specifying cable cleats?
Tried, tested and trusted
We already know that many cable cleats look similar. Even someone with years of experience can find it hard to tell the difference. So how do you differentiate? The answer is that you need to look at the company behind the product. What is their depth of technical know-how? Will they be able to help if things go wrong? What is the provenance of the product you are interested in, how many have been made, and have they been used in similar circumstances? What do others in your industry say about them? Will they deliver on time?
Mechanical strength & short-circuit testing
Knowing the strength of a cable cleat prior to specification is imperative, but it needs to have undergone a short-circuit test for this value to be correct - and this may not be the case. Instead, a cleat’s quoted strength can be arrived at through the use of a mechanical tensile machine, which can be misleading because the force is applied in a slow and controlled manner, unlike in a short-circuit fault, where forces are applied almost instantaneously and oscillate in every direction.
In our experience, a short-circuit test is the only reliable way of proving that a cable cleat is capable of withstanding a specific set of fault conditions and is therefore suitable for specification and installation.
In contrast, a cleat that passes a mechanical tensile test at a given force will not necessarily survive a short-circuit test at the same force.

Pictured: ELLIS Patents Cable Cleats undergoing short-circuit testing. All ELLIS Patents Cable Cleats undergo short circuit testing prior to being brought to market.
Cleat spacing
Cleats also need to be correctly spaced to ensure optimal performance and best value.
In order to calculate this, the system peak fault current and the cable diameter both need to be known. Then by following the formula in FIG 1, which appears in the International Standard (IEC 61914), the forces between two conductors in the event of a three phase fault can be calculated.

Once the value of F in N/m has been determined, then the optimum cleat spacing is easily calculated.
Prior to the cleat and its spacing being finalised it’s important to be aware of two other factors. Firstly, irrespective of the short circuit level, it is strongly recommended that a system employs a fault rated retention device at a maximum spacing of 1,500mm. Secondly, when installing systems on bends and risers, it is recommended that a maximum spacing of 300mm is used.
Matters of corrosion
The risk of material corrosion, either as a result of the installation environment or from other metals the cleat is in contact with, also needs to be given due consideration.
Galvanic corrosion occurs when dissimilar metals are placed in contact with each other in the presence of an electrolyte, and there are two factors that affect its rate. The first being the distance between the two metals in the galvanic series; and the second the relative surface areas of the different metals.
Unfortunately, galvanic corrosion is not easily predictable and can be influenced by the type of electrolytes present - e.g. those coming from salt water or fresh water containing impurities - and so in general terms the safest course of action is to separate dissimilar metals with polymer separation washers. This separation should be carried out between the cleat and its mounting surface, and the cleat’s closure fixing and mounting fixings.
Stainless steel is the material of choice for the vast majority of cable cleats and fixings due to its non-magnetic and corrosion resistant properties, with 304L and 316L being the most commonly used variants.
The corrosion resistance properties of stainless steel are a result of chromium, which reacts with oxygen and forms a self-healing impervious layer of chromium oxide on the surface of the steel. In most circumstances this layer is extremely durable, but in certain locations, such as railway tunnels, the oxide layer can be penetrated as a result of mild steel dust in the atmosphere, which reacts with moisture to exaggerate corrosion. In such circumstances Aluminium products or electrostatic plastic coatings should be used.
Contracts often require a guarantee regarding the life expectancy of a cleat. This is relatively simple if the installation is designed correctly and all other corrosion issues have been considered. Where it becomes complicated is if the cleat or its fixings are manufactured from galvanised mild steel. In such situations, the thickness shown on the Galvanizers Association map, which highlights corrosion rates across the UK, should be referred to and a calculation made as to the necessary thickness of the galvanised / zinc coat.
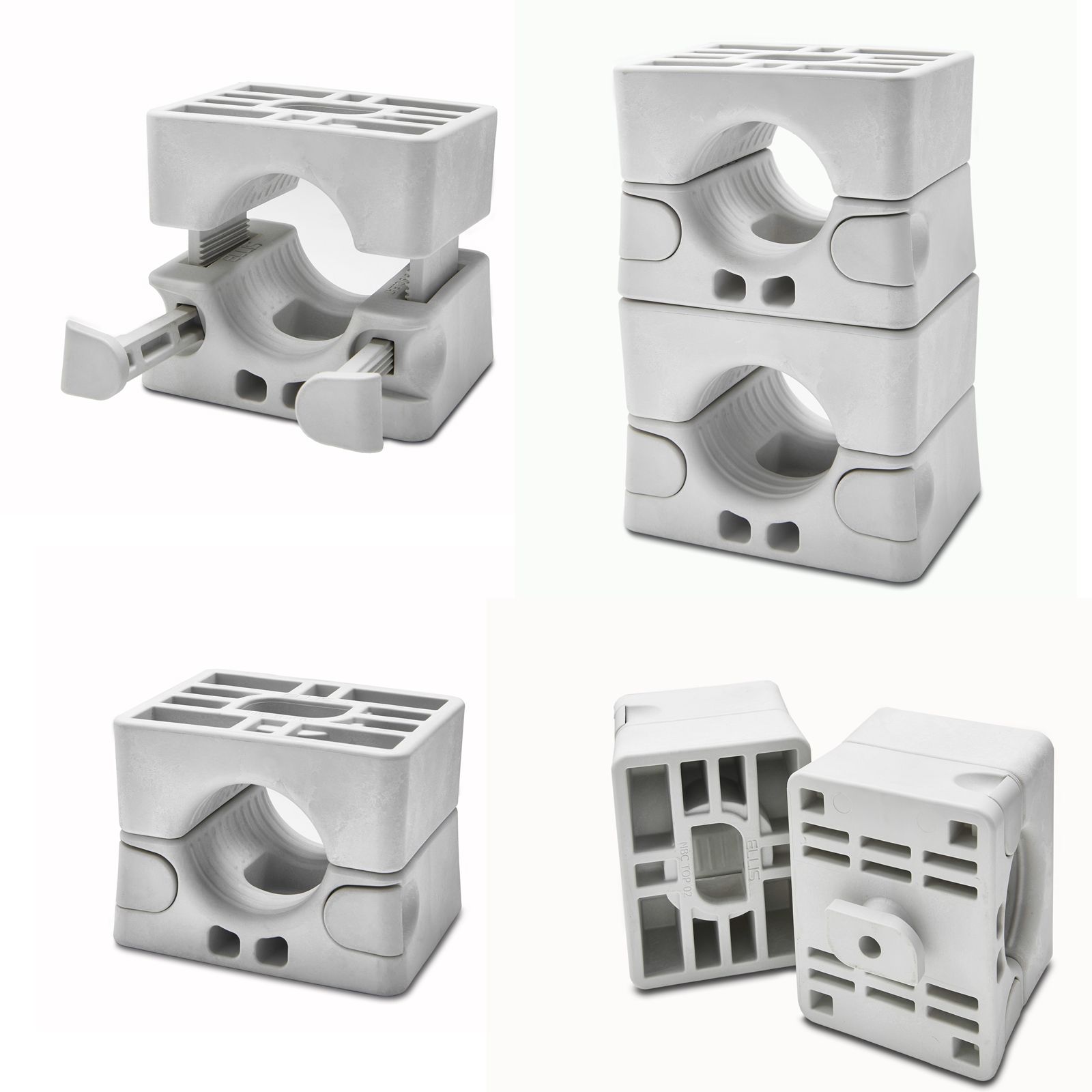
Pictured: ELLIS Patents No Bolts Cleat, fully polymeric and thus resistant to corrosion.
Other elements that should be considered when specifying cleats include:
- Fire - there are no current standards for fire rated cable clamps, but common sense dictates the cleat being used should have the same fire retardancy as the cable.
- Operating temperatures - most cleats are designed for use in ambient temperatures ranging from -50°C to +60°C and with cable conductor temperatures up to 90°C.
- UV resistance - metal cleats are impervious to UV attack. Composite and polymer products aren’t. If they’re likely to be exposed they should be supplied in materials containing carbon black or other UV stabilised additives.
ELLIS Patents is the only leading manufacturer in the global electrical industry that focuses solely on cable cleats.
Contact OHUG Power Equipment for more details on ELLIS Patents products, view our range of ELLIS products here, visit www.ellispatents.co.uk, or follow @ellispatents on Twitter.
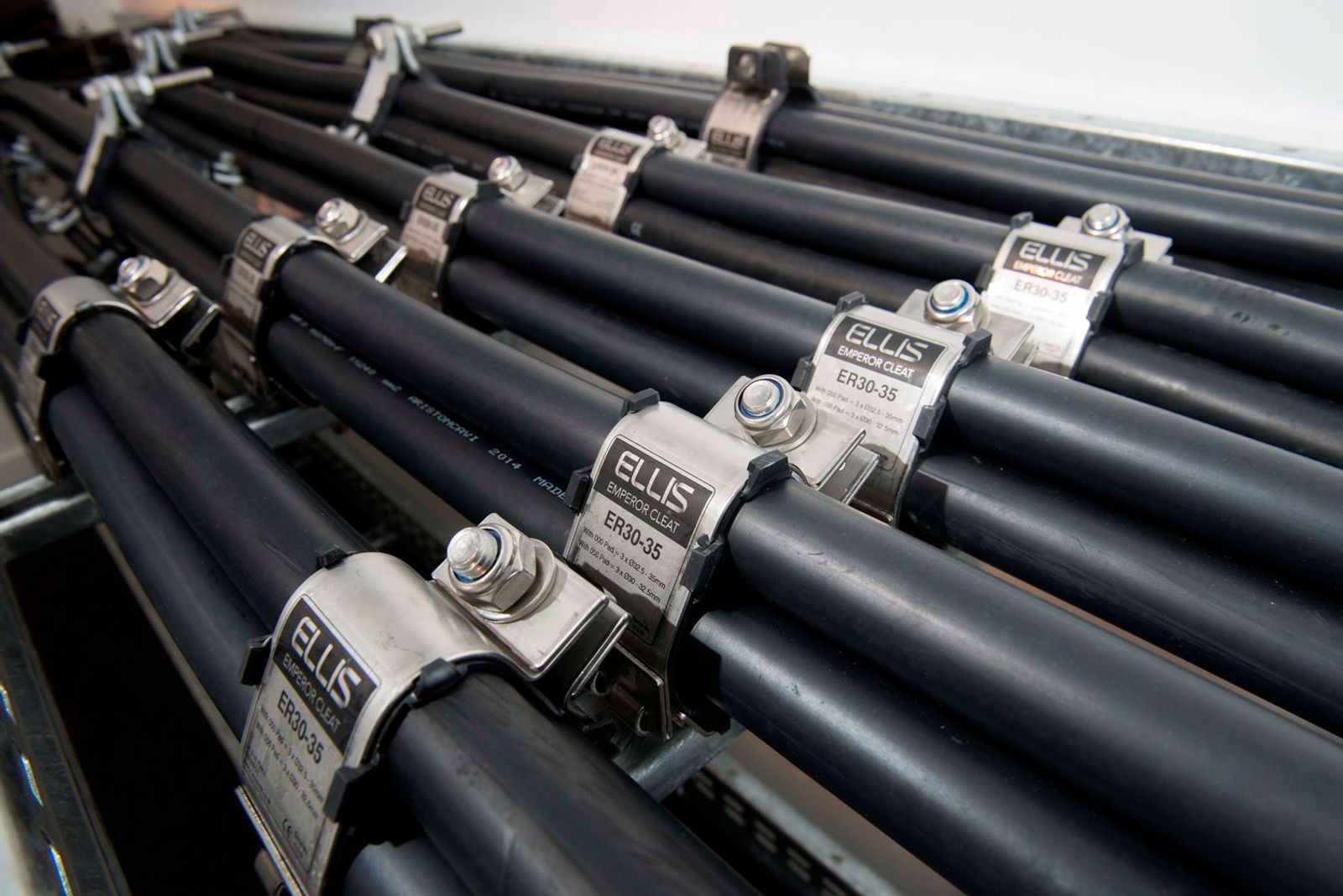

Pictured: ELLIS Patents Emperor Cable Cleats - a market favourite, ELLIS's Emperor cleat has ruled the market for years.
Image Credits: All images supplied by ELLIS Patents.
ELLIS Press Contacts: Daniel Kennedy or Kennady Caines at Source Marketing
T: +44(0)113 380 1644 E: [email protected] / [email protected]
Article originally published & provided by Daniel Kennedy at Source Marketing.